Owning heavy equipment comes with its own unique set of challenges. Big projects mean big payoffs, but they also come with the risk that you’ll need to call in a dealer repair technician – and fork over large sums of money for their expensive travel and repair fees – if something goes wrong. But what if we told you there was another way? In this post, we’ll dive into why doing your own diagnostics in house is often more cost-effective than hiring a dealer repair tech – and how it can help you save money without sacrificing quality performance from your heavy equipment.
When it comes to dealing with heavy equipment breakdowns, paying a dealer to come to your shop or job site can be a major cost. Not only can they charge exorbitant hourly or per-job fees, but they also often have you pay for parts and materials that you could have bought yourself at a lower cost. Furthermore, many dealers will take their sweet time getting to your location.
In house repairs can be more cost-effective than hiring a dealer repair tech because they not only can you save on labor costs, but you are also able to purchase the parts and materials needed at lower prices. Furthermore, when you handle the repairs yourself, you do not have to worry about having to wait around for a dealer to send out a technician.
Time = Money
Time is money in any business, but when it comes to running a fleet of heavy equipment, time can be the difference between success and failure. When an important piece of machinery breaks down unexpectedly and you have to wait for the dealer repair tech to come out, precious time is lost – and that can cost your business dearly. Not only are you unable to complete projects on schedule, but costly delays also lead to customer dissatisfaction and lost profits. In house repairs can help save both time and money by allowing you to quickly identify the problem, purchase parts at lower prices than dealerships charge, and get back up and running faster. Another factor to consider is that you can schedule the repair to fit your schedule rather than being fit into the schedule of a dealership.
Better Repair Options Are Out There!
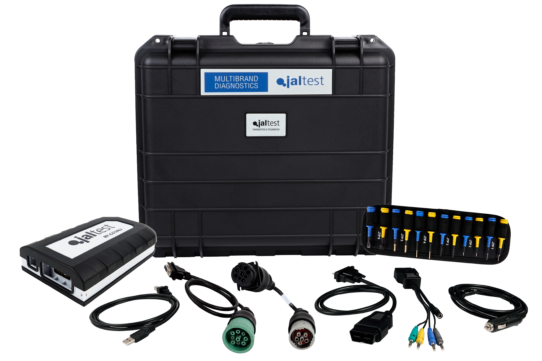
Fleet managers should consider buying their own diagnostic software to troubleshoot and repair their heavy equipment, rather than relying on outside dealer repairs. Jaltest offers an excellent diagnostic software and hardware. Their software also includes the Info Web, which provides the latest in diagnostic troubleshooting & step-by-step repair procedures
To make it even better, the Jaltest software is updated 3 times per year, so you always have the latest information from their engineering team. To top it off, Jaltest has a support team available to assist you if you get into a pinch. Having this kind of support to fall back on when things go wrong is invaluable.
Investing in Jaltest diagnostic software can provide significant cost savings and increased efficiency for those who rely on equipment to operate their businesses or manage their fleet. With Jaltest diagnostic software, individuals, shops and fleet operators can diagnose equipment problems quickly and accurately, without the need to wait for a dealer to arrive on-site. Jaltest diagnostic software can also provide detailed reports on equipment performance, allowing users to identify potential issues before they become significant problems. Additionally, owning diagnostic software can give individuals greater control over the repair process, allowing them to make more informed decisions and potentially save money by handling the repairs themselves or by negotiating with repair technicians. Overall, purchasing diagnostic software is a smart investment for anyone looking to streamline their equipment maintenance processes and save time and money in the long run.
We’ve been setting folks up with Jaltest Off-Highway software for years, contact us today and let’s see how Jaltest can positively impact your business!